The basic elements of the belt conveyor are:
- Belt and belt-tightening system
- Belt drive and power supply
- Roller supports for belt
- Feeding arrangement
- Discharge arrangement
Table of Contents
Principle
Belt conveyors have been used to transport solid materials and bulk objects at high speed. The belt conveyors are based on the principle of material transport from the point of feeding to the point of discharge by a rotating belt driven by a motor in pulleys.
Construction
The basic element of belt conveyors is belt and belt-tightening system, belt drive and power supply, roller support, feeding arrangement, and discharge arrangement. The belt consists of a core or carcass of various plies of cotton duck in which each layer is impregnated and bonded with rubber. The carcass is also coated with a thin rubber layer that joins plies with each other. The belt runs either in the horizontal or inclined position. The belt runs continuously because both ends of the belt are joined to each other.
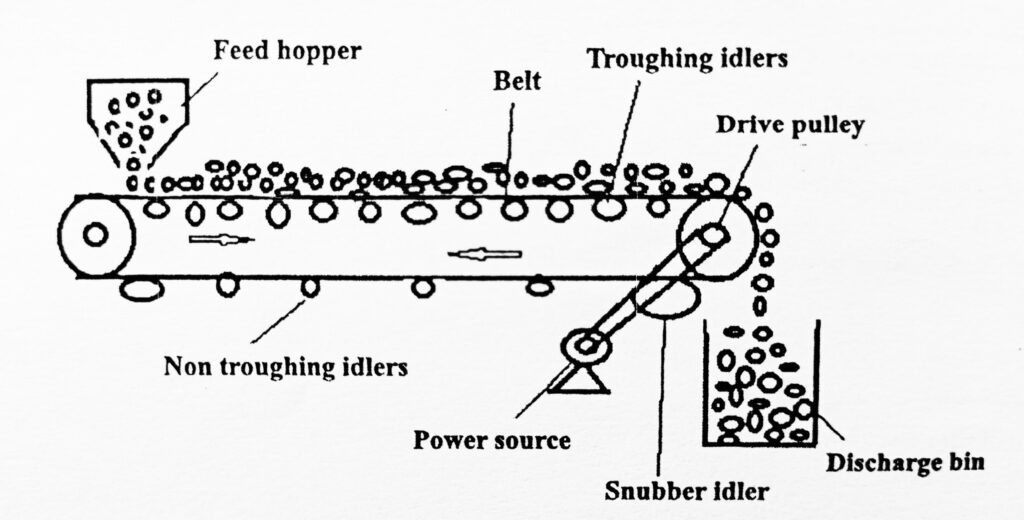
To handle highly abrasive material, a special grade of rubber belts is preferred. The belt of superior quality is made of neoprene and Teflon. Cord belts are also available. The belt should not be too thin or too thick because if the belt is too thin for its width it will sag between idlers and if the belt is too thick then it will not trough properly.
Due to temperature and humidity, the length of the belt is increased. Therefore tighteners are attached to maintain uniform stress on the belt in all conditions. The belt drive is used to move the belt. The simplest device used to drive a belt is a bare steel pulley actuated with the power source. The area of contact between belt and pulley can be enhanced by introducing snubber idlers below the pulley.
Rollers that are arranged on the shaft are used to support the belt and these are called Idlers. There are a significant number of idlers on a conveyor. The selection of the correct type of idlers is very important with respect to the optimum load-carrying capacity of a conveyor and the environment in which the conveyor is to operate. The idlers are troughed to rise belt at edges and depress from the center.
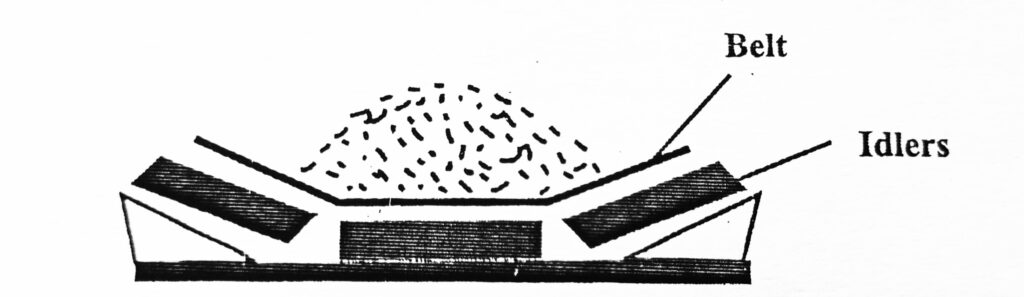
The feed hopper is also attached at one end. Hopper is used to loading feed at the center of the belt. To remove sticky material from the belt, revolving brushes and rubber scraper blades are used. The material on the other side is collected in the discharge bin.
Working
When a rotor rotates, the conveyor belt will also rotate due to the intense friction between the rotor wheel and the belt. This rotating movement of the rotor causes one side of the belt to move in one direction, while the other side moves in the opposite direction. There should be close contact between pulley and belt Therefore snubber idlers are used to maintain close contact between them. The material or feed with the help of the hopper is loaded from one side to the center of the belt. As the belt moves continuously in the forward direction. This also allows the material to travel over the belt in the same direction. The material is collected in the discharge bin from the end of the belt, either mechanically or manually. The selection of belt conveyors depends on the speed of the belt, width of the belt, the power required, mechanical and strength of the belt system, trough ability of the belt, and also material size.
Pharmaceutical Applications
Belt conveyors are used in transporting containers for filling, capping, sealing, labeling, pasting, visual inspection, etc., in the production of injectables, liquid orals, ointments, and jellies.
In the strip and blister packings of tablets and capsules. strips are conveyed on a moving belt. During this process, the strips are packed in cartons.
Belt conveyors are used in the manufacture of lozenges. It is a continuous process of candy base cookies. When a mass of sugar base is on the conveyor, the water is removed. At the end of the belt, the candy base is mixed, tempered, formed, roped, melted, acidulants, and flavors are added, cooled, and sized.
Advantages:
- Belts can be made of asbestos fibers, neoprene, Teflon, and vinyl polymer. Cord belts are also used.
- Belt conveyors are for general purpose installation and are available in relatively large sizes. These can travel several kilometers as in the case of coal mines.
- Routine maintenance of the belt conveyor is easy.
- The Belt conveyor is economical in terms of cost per unit tonne that it can handle.
Disadvantage:
- The Belt conveyor is expensive.
Selection of Belt Conveyor
The capacity of a belt conveyor depends on the cross-section of the load and the speed of the belt. The cross-section of the load depends on the width and slope of the belt and the size of the material. The selection of a belt conveyor depends on:
- Power required.
- Mechanical and tensile strength of the belt system to handle the wide variety of materials.
- Lump size.
- Troughability of the belt.
- The ability of the belt to support the load between idlers.
- Chemical resistance of the belt to the material to be handled.
Manufacturers of belt conveyors publish charts or formulae for the construction of conveyors, size, and power requirements…
Make sure you also check our other amazing Article on : Vacuum Crystallizer